Supply Chain Bottleneck

In the dynamic world of supply chain management, the term "bottleneck" holds significant importance. It refers to a critical point of congestion or constraint within a supply chain network, where the smooth flow of goods and services is hindered, leading to potential disruptions and delays. Understanding and addressing supply chain bottlenecks is crucial for businesses aiming to optimize their operations, enhance efficiency, and meet customer demands effectively.
The Impact of Supply Chain Bottlenecks

Supply chain bottlenecks can have far-reaching consequences, impacting various aspects of a business’s operations and performance. From increased costs and decreased productivity to delayed deliveries and dissatisfied customers, the effects of bottlenecks can be widespread and detrimental. In today’s fast-paced and competitive business landscape, even minor disruptions can lead to significant losses and reputational damage.
Moreover, supply chain bottlenecks often result in a ripple effect, affecting not only the immediate supply chain partners but also the entire ecosystem. For instance, a bottleneck at a manufacturing facility can impact the availability of raw materials for downstream suppliers, leading to further delays and inefficiencies. This interconnectedness underscores the need for a comprehensive understanding and proactive management of supply chain bottlenecks.
Identifying Common Bottlenecks

Identifying the specific bottlenecks within a supply chain is the first step towards addressing them effectively. While bottlenecks can manifest in various forms, some common areas of congestion include:
- Production Delays: Inefficiencies or equipment failures within manufacturing processes can lead to significant production delays, impacting the entire supply chain.
- Logistical Constraints: Issues such as limited warehouse capacity, inadequate transportation infrastructure, or challenges in coordinating cross-border shipments can create logistical bottlenecks.
- Raw Material Shortages: Fluctuations in the availability of raw materials, whether due to seasonal variations, geopolitical factors, or supplier-related issues, can disrupt the supply chain and cause bottlenecks.
- Regulatory and Compliance Hurdles: Complex and ever-changing regulatory landscapes, especially in international trade, can introduce bottlenecks as businesses navigate compliance requirements.
- Labor Shortages and Skill Gaps: A shortage of skilled labor or an inability to meet labor demands can slow down operations and create bottlenecks, particularly in industries with high labor intensity.
Recognizing these common bottlenecks is essential, but it's equally crucial to analyze the unique aspects of each supply chain to identify specific pain points that may be hindering performance.
Strategies to Mitigate Supply Chain Bottlenecks
Addressing supply chain bottlenecks requires a multifaceted approach, combining strategic planning, technological advancements, and collaborative efforts across the supply chain network. Here are some effective strategies to mitigate the impact of bottlenecks:
Enhanced Forecasting and Demand Planning
Accurate forecasting and demand planning are fundamental to preventing supply chain bottlenecks. By leveraging advanced analytics and historical data, businesses can predict demand patterns, identify potential shortages, and optimize inventory levels accordingly. This proactive approach ensures that supply chain partners have the necessary resources to meet demand without overburdening the system.
Robust Supply Chain Visibility
Implementing real-time tracking and visibility solutions enables supply chain stakeholders to monitor the movement of goods, identify potential delays, and make informed decisions. With enhanced visibility, businesses can quickly identify bottlenecks, whether they occur in production, transportation, or inventory management, and take immediate corrective actions.
Flexible Sourcing and Supplier Management
Building a diverse and resilient supplier network is crucial for mitigating supply chain risks. By diversifying suppliers and exploring alternative sourcing options, businesses can minimize the impact of bottlenecks caused by raw material shortages or supplier-related issues. Additionally, implementing robust supplier management practices, including regular audits and performance evaluations, ensures that suppliers meet quality and delivery standards, reducing the likelihood of disruptions.
Streamlined Logistics and Transportation
Optimizing logistics and transportation processes is essential for overcoming supply chain bottlenecks. This involves leveraging technology to streamline route planning, optimize vehicle utilization, and reduce transportation costs. Additionally, exploring alternative transportation modes, such as intermodal shipping or utilizing emerging technologies like drones for last-mile deliveries, can enhance efficiency and reduce congestion.
Collaborative Planning and Shared Insights
Encouraging collaboration and information sharing among supply chain partners can lead to more efficient operations. By sharing demand forecasts, inventory levels, and production schedules, businesses can align their processes, anticipate potential bottlenecks, and develop joint strategies to mitigate risks. This collaborative approach fosters a sense of shared responsibility and enables a more agile response to supply chain challenges.
Case Study: Overcoming Bottlenecks in the Automotive Industry
The automotive industry, known for its complex supply chains and just-in-time production models, provides an insightful example of overcoming supply chain bottlenecks. One prominent bottleneck faced by automotive manufacturers is the procurement and management of a vast array of components and parts from diverse suppliers.
To address this challenge, leading automotive companies have adopted advanced technologies such as AI-powered supply chain optimization platforms. These platforms analyze historical data, market trends, and supplier performance to optimize procurement processes, identify potential shortages, and suggest alternative sourcing options. By leveraging these insights, manufacturers can proactively manage their supply chains, reduce lead times, and minimize the impact of bottlenecks.
Additionally, the automotive industry has embraced collaborative planning and shared insights among supply chain partners. Through industry forums and digital platforms, manufacturers, suppliers, and logistics providers share real-time data, collaborate on demand forecasting, and develop joint strategies to ensure a seamless flow of components. This collaborative approach has not only improved efficiency but also fostered a culture of continuous improvement within the industry.
The Future of Supply Chain Bottleneck Management

As supply chains become increasingly complex and interconnected, the management of bottlenecks will continue to evolve. Emerging technologies, such as blockchain, Internet of Things (IoT), and artificial intelligence, are poised to play a pivotal role in enhancing supply chain visibility, optimizing processes, and mitigating risks.
Blockchain, for instance, offers a decentralized and transparent ledger system, enabling secure and tamper-proof data sharing among supply chain partners. This technology can enhance traceability, improve inventory management, and reduce the likelihood of bottlenecks caused by information asymmetry or fraud. Similarly, IoT devices and sensors can provide real-time data on the movement and condition of goods, enabling proactive decision-making and reducing delays.
Furthermore, the integration of AI and machine learning algorithms can revolutionize supply chain planning and optimization. These technologies can analyze vast amounts of data, identify patterns, and make predictive recommendations to mitigate bottlenecks. By leveraging AI-powered analytics, businesses can optimize inventory levels, improve production planning, and enhance overall supply chain resilience.
Industry | Bottleneck Type | Potential Solution |
---|---|---|
Automotive | Component Sourcing | AI-powered Optimization Platforms |
Healthcare | Supply Shortages | Blockchain-based Traceability |
E-commerce | Logistical Constraints | IoT-enabled Real-time Tracking |
Food & Beverage | Raw Material Fluctuations | Sustainable Sourcing Practices |
Electronics | Production Delays | Lean Manufacturing Techniques |
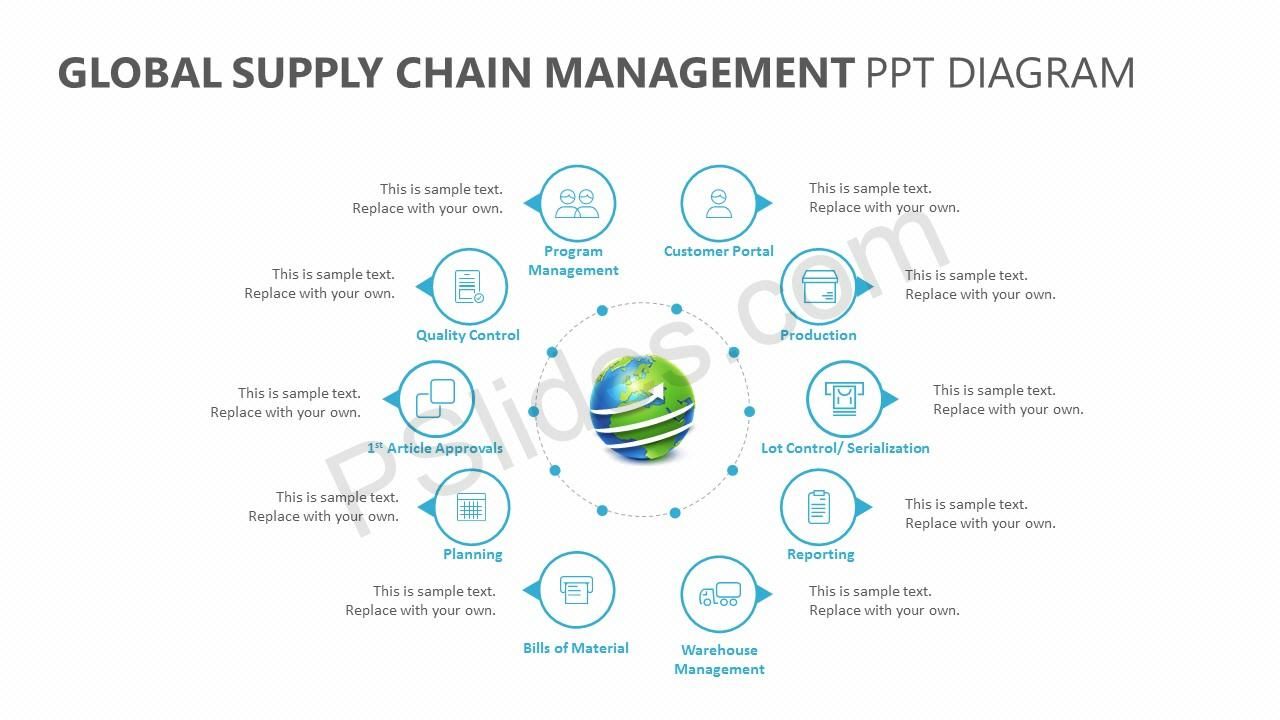
Conclusion
Supply chain bottlenecks are inevitable challenges that businesses must navigate to maintain operational efficiency and customer satisfaction. By understanding the common bottlenecks, adopting proactive strategies, and leveraging technological advancements, organizations can mitigate the impact of these constraints and build resilient supply chains. The future of supply chain management lies in embracing innovation, collaboration, and data-driven decision-making to create agile and responsive ecosystems.
What are the key indicators of a supply chain bottleneck?
+
Key indicators of supply chain bottlenecks include increased lead times, reduced productivity, delayed deliveries, rising costs, and customer complaints. Analyzing these metrics and identifying patterns can help businesses pinpoint specific pain points.
How can businesses prioritize addressing different bottlenecks?
+
Prioritization should be based on the potential impact of each bottleneck on the overall supply chain performance. Factors such as the frequency of occurrence, the extent of disruption, and the criticality of the affected components or processes should be considered when determining the order of addressing bottlenecks.
What role does technology play in managing supply chain bottlenecks?
+
Technology plays a pivotal role in managing supply chain bottlenecks by providing real-time data, advanced analytics, and process automation. Technologies like AI, IoT, and blockchain enhance supply chain visibility, enable predictive analytics, and facilitate collaborative decision-making, ultimately reducing the impact of bottlenecks.