What Is An Exception In Shipping
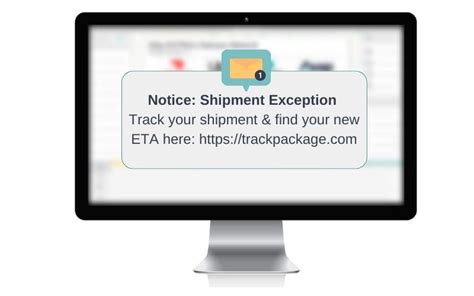
In the intricate world of shipping and logistics, exceptions are inevitable. They represent deviations from the standard flow of a shipment, often causing disruptions and delays. These exceptions can arise from various factors, including errors in data entry, unexpected weather conditions, changes in customer requirements, or issues with customs and documentation. Understanding and effectively managing exceptions is crucial for maintaining smooth operations and ensuring customer satisfaction.
The impact of exceptions can be significant, affecting not just the delivery timeline but also the overall cost and resource allocation. For instance, a simple mistake in the shipping address can lead to a package being returned to the sender, resulting in additional expenses and a dissatisfied customer. Similarly, unexpected customs delays can cause a ripple effect, impacting the entire supply chain and potentially leading to financial losses.
Defining an Exception in Shipping

An exception in shipping refers to any event or circumstance that deviates from the normal, expected flow of a shipment. It is a situation that requires special attention and often demands immediate action to resolve. These exceptions can occur at any stage of the shipping process, from the initial pickup to the final delivery, and can have a wide range of causes and implications.
Some common examples of shipping exceptions include:
- Late or missed deliveries
- Damaged or lost packages
- Address or delivery location errors
- Customs delays or issues
- Unforeseen weather conditions affecting transport
- Changes in customer instructions or requirements
- Technical glitches in tracking or logistics systems
The Impact of Shipping Exceptions
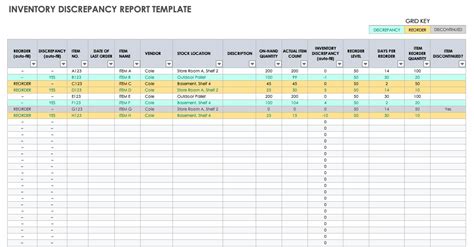
Shipping exceptions can have far-reaching consequences, affecting not only the specific shipment but also the broader logistics network and the business as a whole. Here are some key areas where exceptions can create significant impacts:
Operational Disruptions
Exceptions can disrupt the smooth flow of operations, causing delays in delivery schedules. This can lead to a backlog of shipments, increased pressure on logistics teams, and potential damage to the company’s reputation for timely deliveries.
Financial Implications
The financial costs associated with exceptions can be substantial. This includes expenses related to reshipments, additional storage fees, customs penalties, and even legal costs in case of severe delays or losses. Furthermore, exceptions can also impact a company’s bottom line through lost sales and reduced customer loyalty.
Customer Satisfaction and Loyalty
Shipping exceptions directly affect customer satisfaction. Late deliveries, damaged goods, or incorrect shipments can lead to disappointed customers and negative reviews. This, in turn, can harm a company’s reputation and reduce customer loyalty.
Resource Allocation and Planning
Exceptions require additional resources to manage and resolve. This can strain a company’s logistics capabilities, especially if exceptions are frequent or complex. It can also disrupt long-term planning and forecasting, making it harder to optimize resource allocation.
Managing Shipping Exceptions
Effectively managing shipping exceptions is crucial for minimizing their impact and maintaining operational efficiency. Here are some key strategies for exception management:
Robust Tracking and Monitoring Systems
Implementing advanced tracking technologies can help identify exceptions early on. Real-time visibility into the shipment’s journey enables prompt action and can prevent minor issues from escalating into major problems.
Proactive Communication
Keeping open lines of communication with customers, suppliers, and logistics partners is essential. Regular updates and transparent information sharing can help manage customer expectations and allow for timely interventions when exceptions occur.
Exception Management Protocols
Developing standardized protocols for handling different types of exceptions can streamline the process. This includes defining roles and responsibilities, setting clear escalation paths, and establishing guidelines for decision-making.
Training and Education
Providing comprehensive training to logistics staff on exception management can enhance their ability to handle complex situations. This includes understanding the root causes of exceptions, effective communication strategies, and the use of technology to resolve issues.
Continuous Improvement
Regularly reviewing exception data and performance can identify areas for improvement. Analyzing trends and patterns can help in predicting and preventing future exceptions, as well as optimizing the exception management process.
Future Trends in Exception Management
The field of exception management is rapidly evolving, driven by advancements in technology and changing customer expectations. Here are some key trends to watch out for:
Artificial Intelligence and Machine Learning
AI and machine learning algorithms can analyze vast amounts of data to identify patterns and predict potential exceptions. This can enable proactive measures to prevent exceptions and improve overall logistics efficiency.
Blockchain Technology
Blockchain offers a secure and transparent way to track shipments and manage exceptions. It can provide an immutable record of events, making it easier to identify and resolve issues quickly.
Internet of Things (IoT)
IoT devices, such as smart sensors and GPS trackers, can provide real-time data on the condition and location of shipments. This can help in early detection of potential exceptions and allow for timely interventions.
Enhanced Customer Experience
With the rise of e-commerce, customer expectations for seamless and fast deliveries are higher than ever. Companies are investing in technologies and processes to minimize exceptions and provide a superior customer experience.
Conclusion
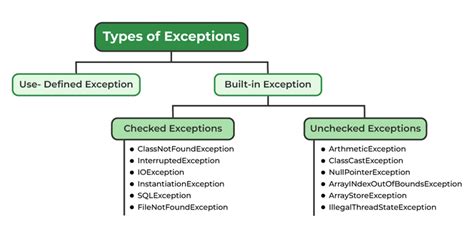
Shipping exceptions are an inevitable part of the logistics landscape. However, with the right strategies and technologies, they can be effectively managed to minimize their impact. By staying ahead of the curve with emerging trends and continuously improving exception management processes, businesses can ensure smooth operations, satisfied customers, and a robust supply chain.
How can I reduce the occurrence of shipping exceptions?
+Reducing shipping exceptions requires a multi-faceted approach. First, ensure accurate data entry and thorough quality checks. Implement robust tracking systems and provide real-time updates to customers and stakeholders. Train your team to handle exceptions promptly and effectively. Regularly review exception data to identify trends and improve processes. Finally, stay updated with industry best practices and leverage emerging technologies to predict and prevent exceptions.
What are some common causes of shipping exceptions?
+Shipping exceptions can arise from various causes, including human error (such as incorrect data entry or packaging mistakes), external factors (like weather disruptions or traffic delays), and operational issues (such as equipment failures or capacity constraints). Additionally, changes in customer requirements or last-minute order alterations can also lead to exceptions.
How do shipping exceptions affect my business’s reputation?
+Shipping exceptions can significantly impact your business’s reputation. Delayed deliveries, damaged goods, or incorrect shipments can lead to dissatisfied customers who may leave negative reviews or even switch to competitors. To mitigate this, it’s crucial to have effective exception management strategies in place, including proactive communication with customers and a focus on delivering a positive customer experience despite unexpected challenges.